1. Large weight range. Forgings are as small as a few grams to as large as hundreds of tons
2. Higher quality than castings. Forgings have better mechanical properties than castings, and can withstand large impact forces and other heavy loads. Therefore, forgings are used for all important and stressed parts.
For high-carbide steels, forgings are of better quality than rolled products. For example, high-speed steel rolled products can only meet the requirements after being reformed for forging. Especially high-speed steel milling cutters must be forged.
3. The lightest weight. On the premise of ensuring design strength, forgings are lighter than castings, which reduces the weight of the machine itself, which is of great significance for transportation, aircraft, vehicles and astronautical equipment.
4. Save raw materials. For example, for a crankshaft with a dead weight of 17kg used in automobiles, when using rolled material for cutting and forging, the chips account for 189% of the weight of the crankshaft, while when using die forging, the chips account for only 30%, which also shortens the machining time by 1/6.
Precision forging forgings can not only save more raw materials, but also save more machining man-hours.
5. High productivity. For example, using two hot forging presses to forge radial thrust bearings can replace 30 automatic cutting machine tools. When the upsetting automatic machine is used to produce M24 nuts, the productivity of the six-axis automatic lathe is 17.5 times.
6. Free forging has great flexibility. Therefore, forging methods are widely used in some repair factories to produce various accessories.
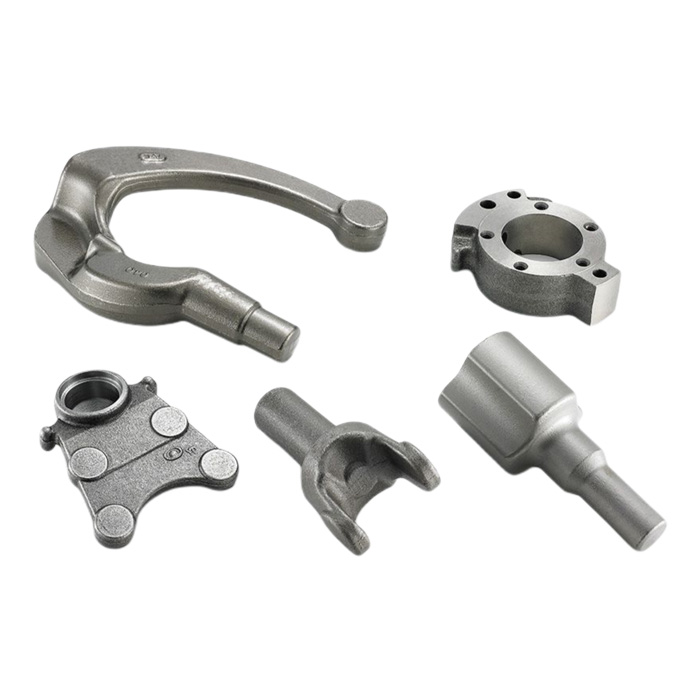